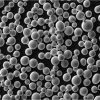
In recent years, it has become possible to use laser beams and electron beams to "print" engineering objects that have complex shapes that could not be achieved by conventional manufacturing routes. The additive manufacturing (AM) process, known widely as 3D printing, for metallic materials involves melting and fusing fine-scale powder particles — each about ten times finer than a grain of local beach sand — in sub-millimeter-scale "pools" created by focusing a laser or electron beam on the material. "The highly focused beams provide exquisite control, enabling 'tuning' of properties in critical locations of the printed object," says Tresa Pollock, professor of materials and associate dean of the College of Engineering. "Unfortunately, many advanced metallic alloys used in extreme heat-intensive and chemically corrosive environments encountered in energy, space, and nuclear applications are not compatible with the AM process." The challenge of disco
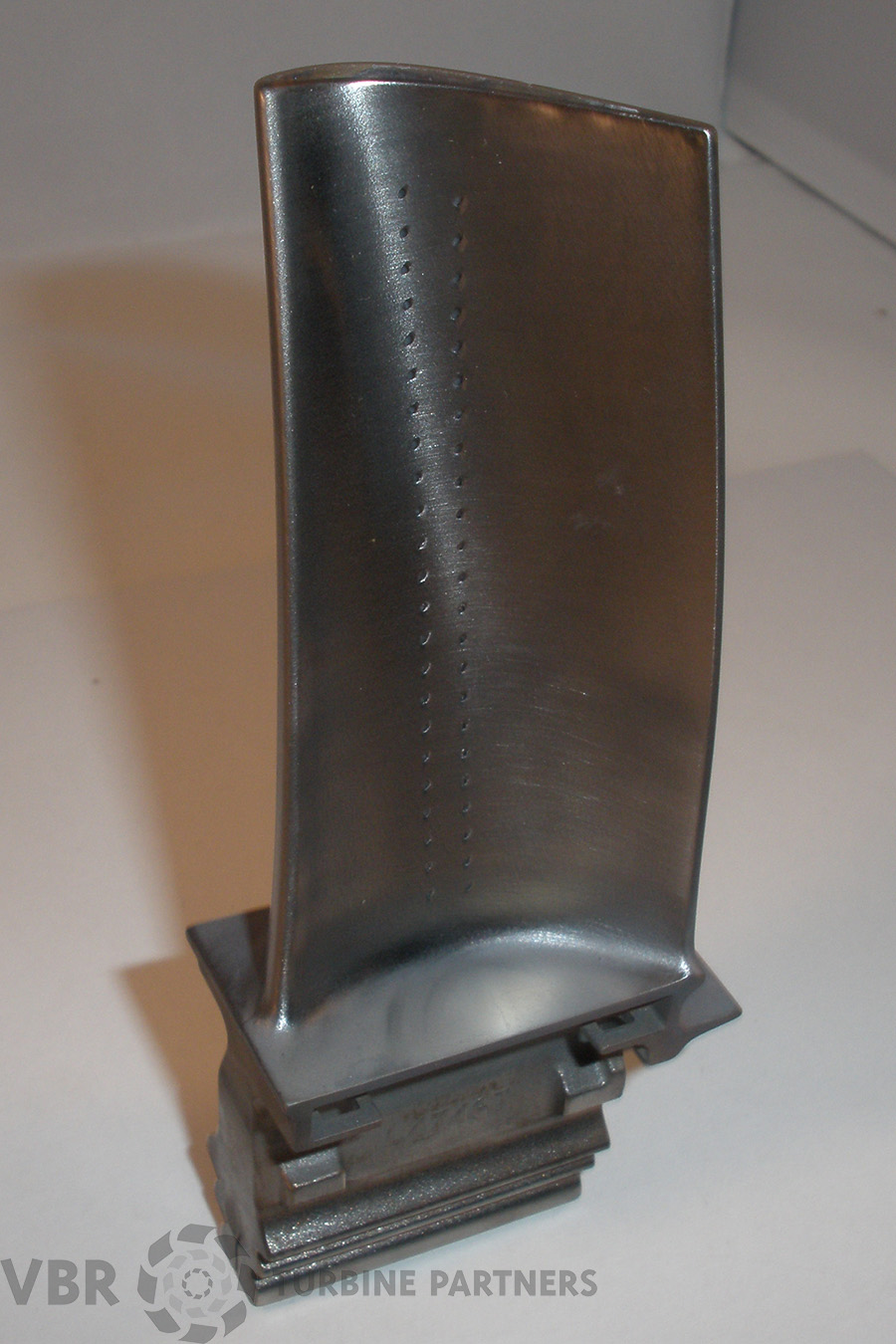
SEM micrographs of metal powder of SB-CoNi-10 used for a EBM and b SLM printing trials. Simple bar geometries have been printed for uniaxial tensile testing c, d in addition to complex geometries such as prototype turbine blades with e internal cooling channels or f thin, over-hanging platforms. IPF maps acquired through EBSD show the grain structure of the as-printed CoNi-base superalloy along the build direction manufactured through g EBM and h SLM. The scale bars for a, b and g, h are 500 μm. The scale bars for c–f are 2 cm. Stronger materials in the metal AM space promise greater applicability across a range of industries. Aerospace is noted up by these researchers, but high-strength and high-heat alloys can also be deployed in diverse military applications. More reliable alloys are, moreover, useful when marketing AM as an industrial solution alongside subtractive manufacturing options. The new alloy is designed to address a common flaw in the metal A
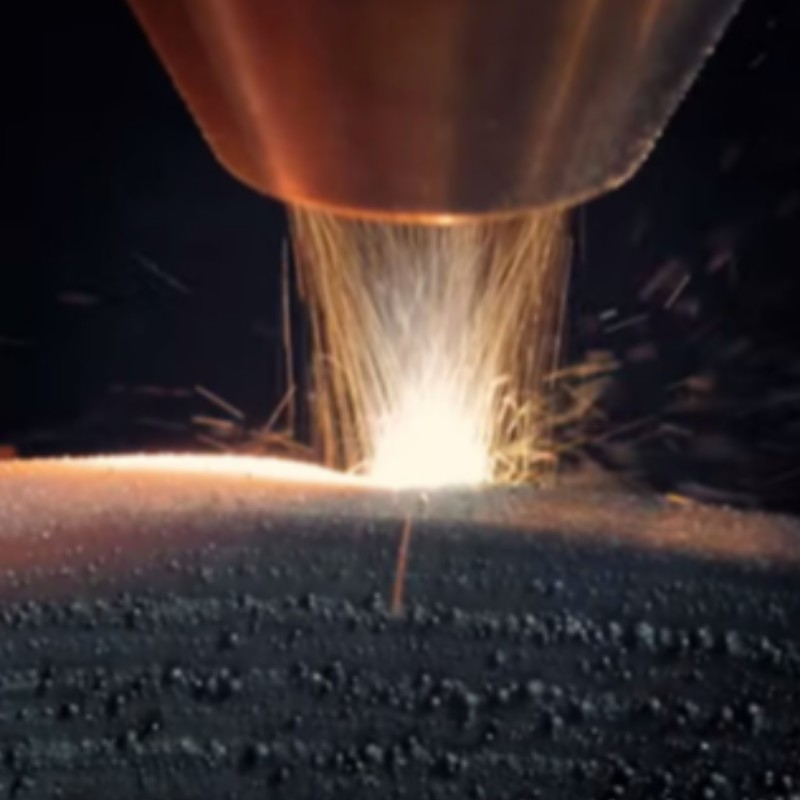
Compared to big data, VR, and artificial intelligence, 3D printing today is actually not a very new technology. This technology has a history of more than 30 years. So how many advantages are there in metal 3D printing? What are the differences between different metal 3D printing technologies in the field of printing materials and metallurgy? In this issue, 3D Science Valley and Gu You come to experience the metallurgy and processing science of metal D printing. Metal printed Origin and next steps One of the earliest 3D printing technologies related to metal additive manufacturing was SLS-selective laser sintering technology, which was used to sinter plastic powder at that time. And in 1990, Manriquez-Frayre and Bourell realized the application of printing metal products through SLS technology. Today, when we mention metal 3D printing, we usually refer to SLM-selective laser melting technology, and SLS technology is more used to sinter materials other than metal. SLM te
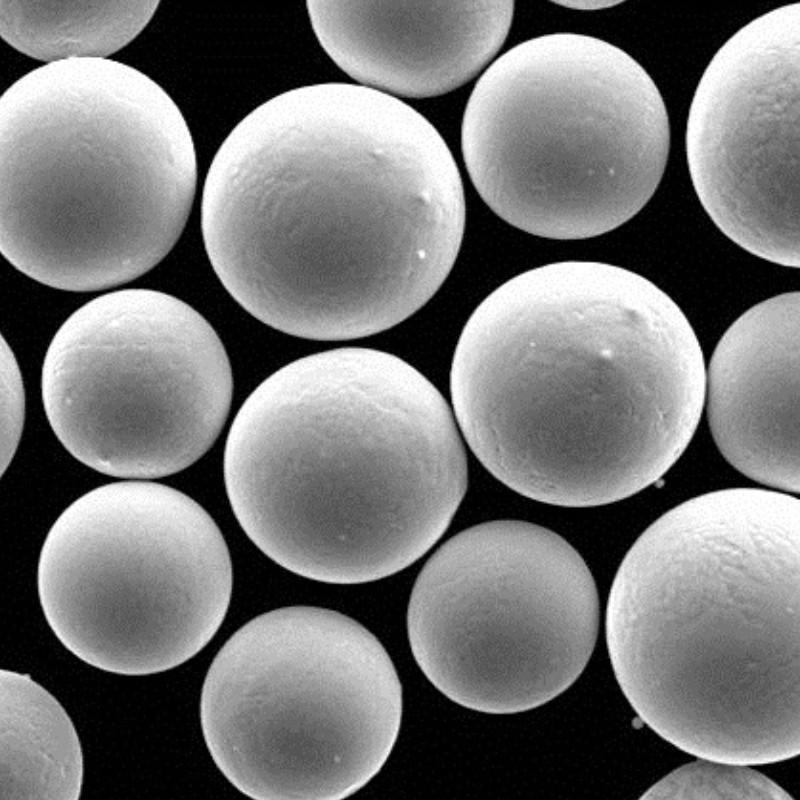
The powder preparation method in which a fast-moving fluid (atomizing medium) impacts or otherwise breaks the metal or alloy liquid into fine droplets and then condenses into a solid powder is called the atomization powdering method. Among the existing pulverizing technologies in my country, the most widely used are water atomization and gas atomization. Although the powdering principle is the same, the physical properties of the powders are still very different. Let's understand the difference between the two. 1. Shape Since the heat capacity of gas is smaller than that of water, when gas atomization is used, the alloy receives a low degree of chill. When the atomization medium is impacted, the alloy liquid atomized into fine droplets will not solidify immediately, which gives the alloy The time for the droplet to shrink into a ball during the falling process, so it is easy to obtain spherical alloy powder. When water is atomized, the situation is just the opposite. Due to the chilli
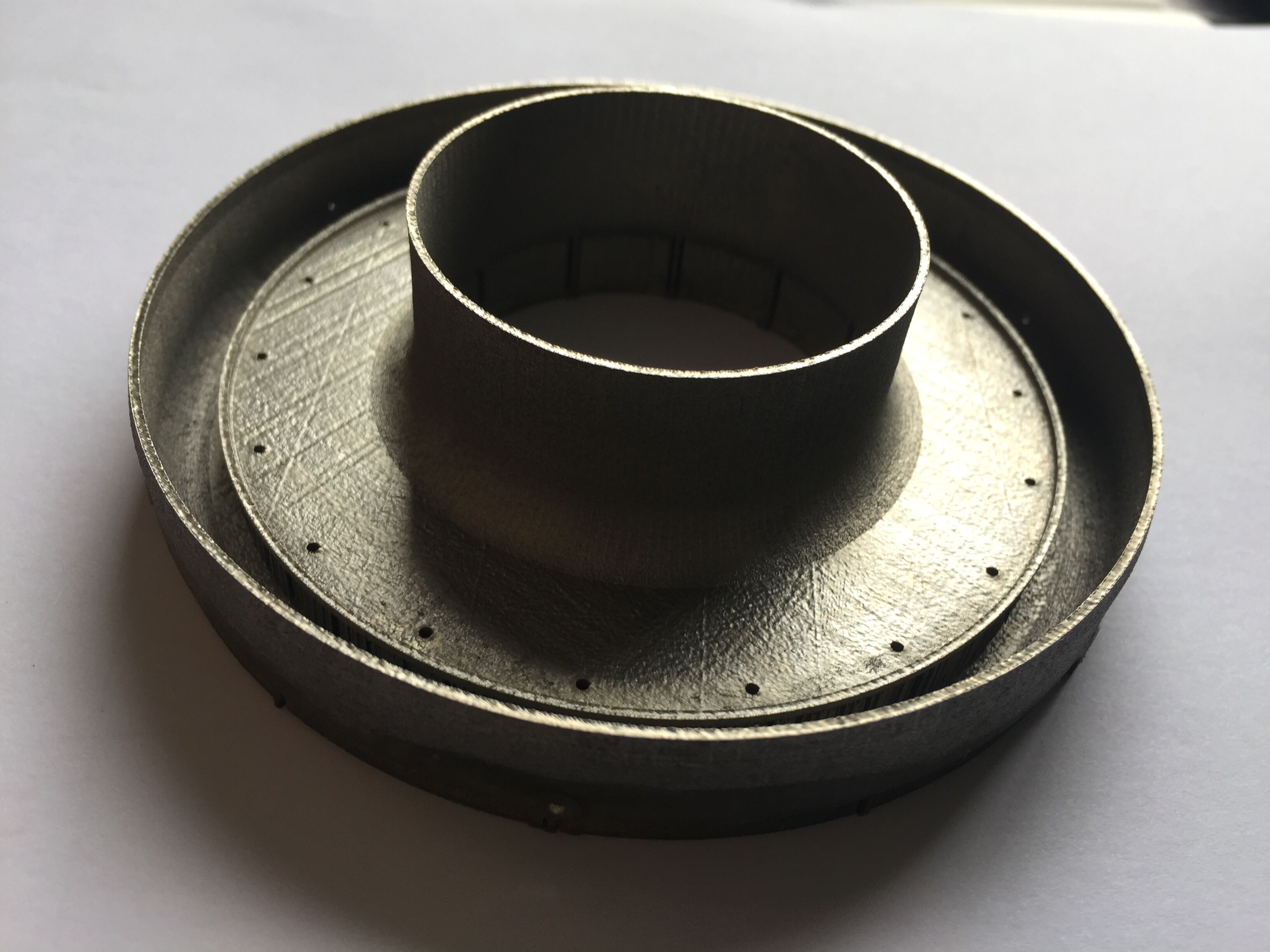
The revolutionary significance of 3D printing is self-evident. Through 3D printing technology, any impossible shape can be magically manufactured. This allows many difficult problems in practical applications to be solved. While providing a perfect solution, the investment is low and the production cycle is shortened. In addition, the remaining nickel alloy powder can be used continuously, avoiding the waste of resources. Alloy 718 is a superalloy based on iron-nickel hardening. It has good corrosion resistance and heat resistance, tensile, fatigue, and creep properties. It is suitable for various high-end applications, such as aircraft turbine engines and land-based turbines. The alloy spherical powder made by Alloy 718 is also called universal powder and is widely used in the field of 3D metal printing. Nickel alloy spherical powder use: 3D printing, injection molding, hot isostatic pressing, spraying Nickel alloy spherical powder material: 718, 625, 4J36, C276, GH4169, GH2132
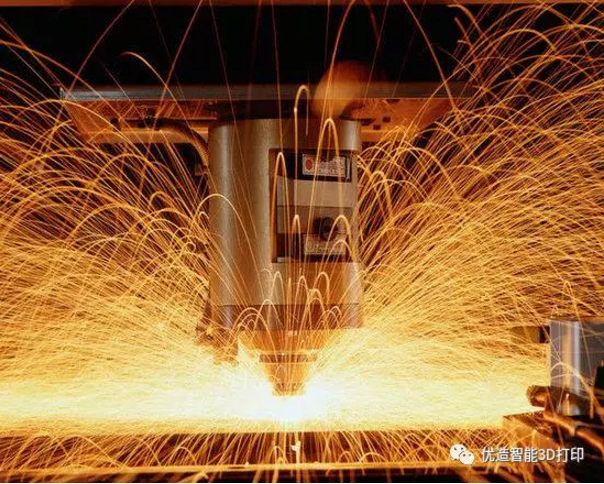
Subtractive molding refers to the use of separation technology to remove excess material from the substrate in an orderly manner. For example, traditional turning, milling, grinding, drilling, planing, electric spark and laser cutting are all subtractive molding. Traditional molding processes such as laser cutting are prone to cause material waves
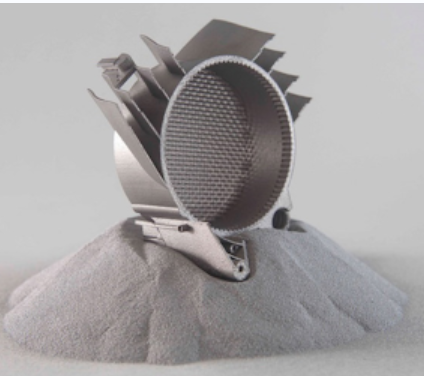
The cost of metal powders for additive manufacturing (AM) is high and contributes an appreciable proportion to the manufactured cost of printed components. While the capital investment associated with a printer is committed, and progressively offset over time, feedstock costs attract ongoing scrutiny. Regular usage is a constant reminder that metal powder supplies attract a high price, particularly when compared to the price of the solid material (bar stock) and highlights the need to extract maximum performance from a feed. A price worth paying? It’s worth noting that there are sound reasons for the high cost of metal AM powders. It largely reflects the production method, most commonly water, gas (nitrogen, argon, or helium), or plasma-based atomisation, which influences vital properties such as particle size and shape. The highly spherical, largely satellite-free, morphology of particles produced by plasma processing, along with excellent purity, typically result in perf
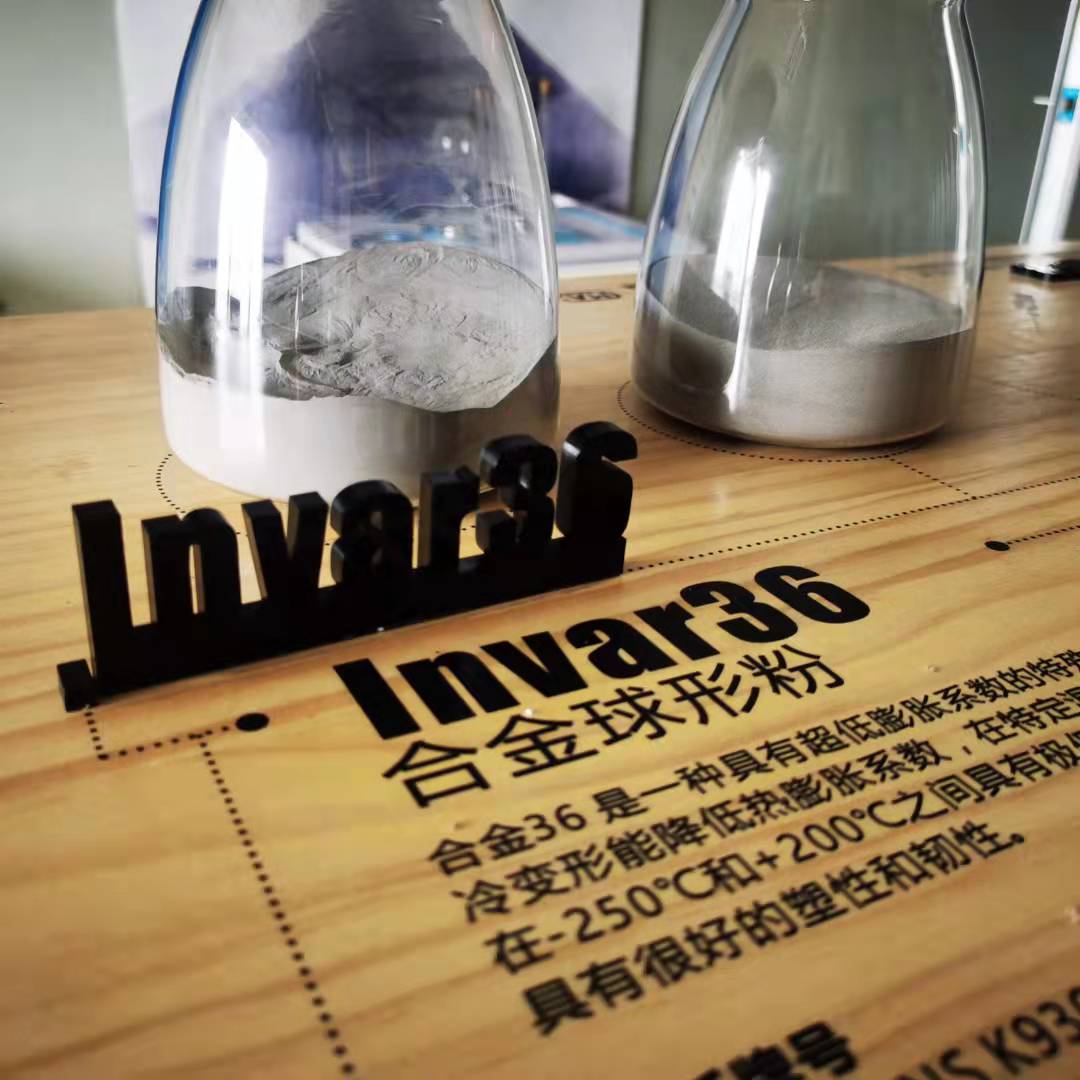
Alloy 36 is a special low-expansion iron-nickel alloy with an ultra-low expansion coefficient. Cold deformation can reduce the coefficient of thermal expansion and stabilize the coefficient of thermal expansion within a specific temperature range. Its polar thermal expansion coefficient is between -250°C and +200°C.<br /> Has good plasticity and toughness
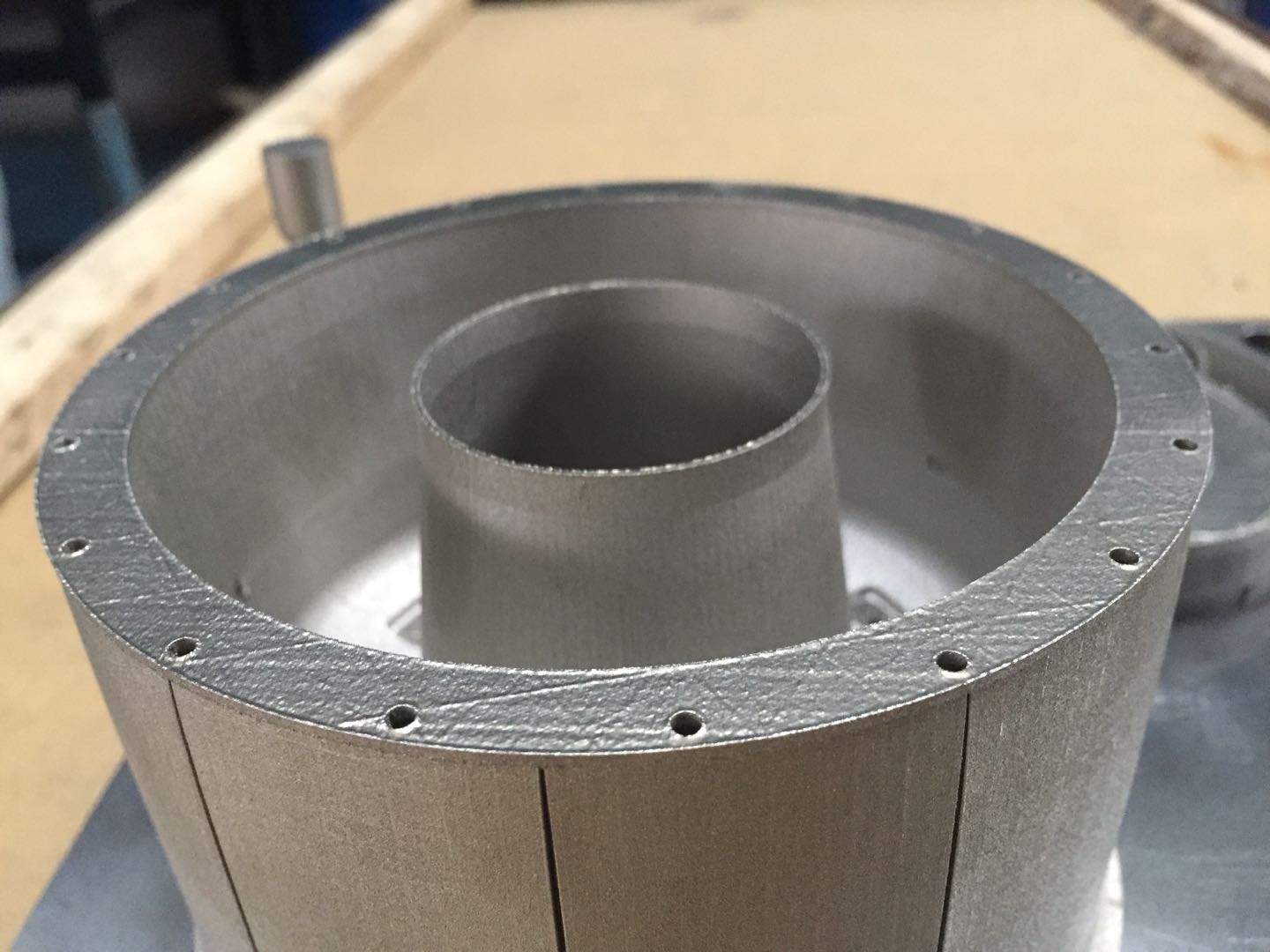
As one of the purest digital manufacturing methods, 3D printing is growing properly every year in terms of market size and development speed.It involves computers and machinery.The most important factor is advanced material science, especially computer materials.Aditive manufacturing automation has the greatest impact. SmarTech's latest publication "3D▁Printing Commission Market-2017:Opportunity Analysis and Ten-Year Forecast provides an in-depth and accurate assessment of 3D printing composers.It is said that by 2026, the global revenue of 3D printing composers will exceed 500 million US dollars, composed the most important market opportunity for 3D printing ten years. Charts of composite materials currently available for 3D printing 3D printing is regarded by the industry as a way to simplify and automate the production process. It preserves the advantages of fiber composite materials in terms of weight optimization and strength. For the polymer 3D printing industry, 3D
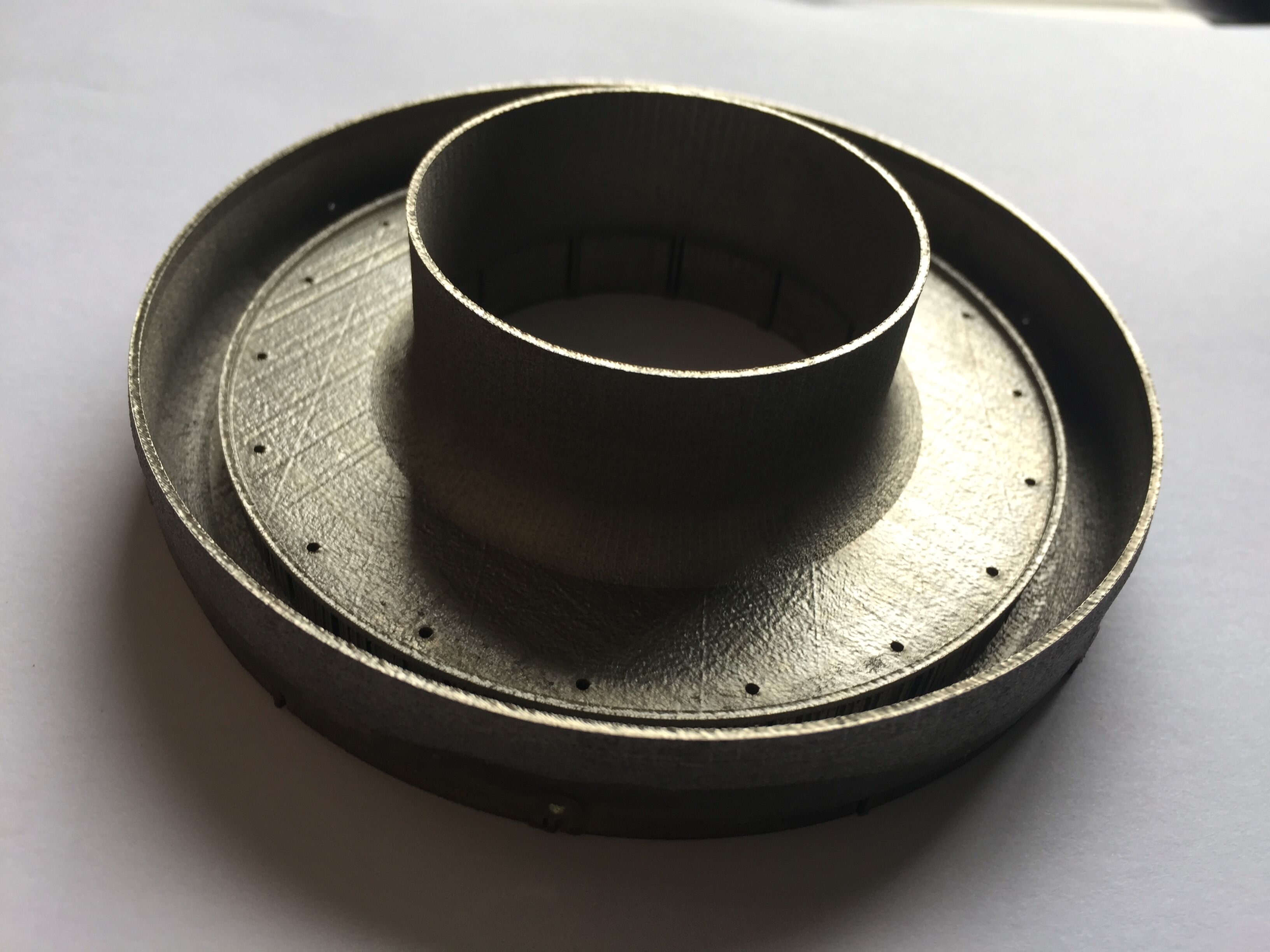
3D printing can effectively manufacture fine structures that are traditionally difficult to achieve without waste, such as the hollow geometry of nickel-based superalloy aerospace parts. In order to take full advantage of this method, we must switch to new alloys and processes. Conventional high-temperature alloy manufacturing Superalloys are a family of metal mixtures based on nickel, cobalt or iron that can resist high temperature deformation, corrosion and oxidation, especially when operating at high temperatures close to their melting point. They were originally developed for gas turbine components in turbojet engines and are now widely used in high temperature applications in the aerospace and power generation industries. In order to achieve these high-temperature characteristics (mechanical and chemical), microstructure control is essential, and specific alloying element additions and careful manufacturing processes can be combined to achieve. Nickel-based superallo
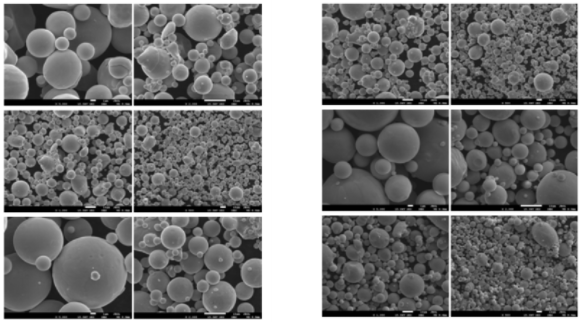
1j79 is a commonly used iron-nickel alloy (soft magnetic alloy), which can also be called Bromo alloy. It mainly achieves sufficient magnetic permeability and magnetic saturation induction through a reasonable combination of nickel and iron. Permalloy often refers to iron-nickel alloys with a nickel content in the range of 30 to 90%. It is a very widely used soft magnetic alloy. Through appropriate technology, magnetic properties can be effectively controlled, such as initial permeability exceeding one hundred thousand, maximum permeability exceeding one million, coercivity as low as two thousandths of Oersted, close to 1 or close to With a zero rectangular coefficient, permalloy with a face-centered cubic crystal structure has good plasticity, and can be processed into 1 micron ultra-thin ribbons, alloy powders and various forms of use. The 1J79 alloy powder independently developed by Shanghai Lanzhu has a spherical shape and features: good fluidity, uniform p

3D printing has been around for longer than most people think - the first 3D print was made in 1981 by Hideo Kodama. But 3D printing has come a long way since then, with prints being made at resolutions as low as two-hundredths of a millimeter. 3D printing is an innovative method of production: a three-dimensional object is visualized in detail using computer software, the data is sent to a 3D printer, and the printer creates it. Almost all consumer printers can only print in plastic, but that won’t be true much longer. Today’s metal fabrication processes involves both a huge amount of energy and a substantial amount of waste: in the manufacture of some products, up to 90% of the metal used is cut away. This involves excessive use of energy as well as metal, besides making the finished product up to 60% heavier than it needs to be, the latter being an expensive handicap in the aviation industry, for instance. 3D printing, in contrast, uses almost precisely as much material
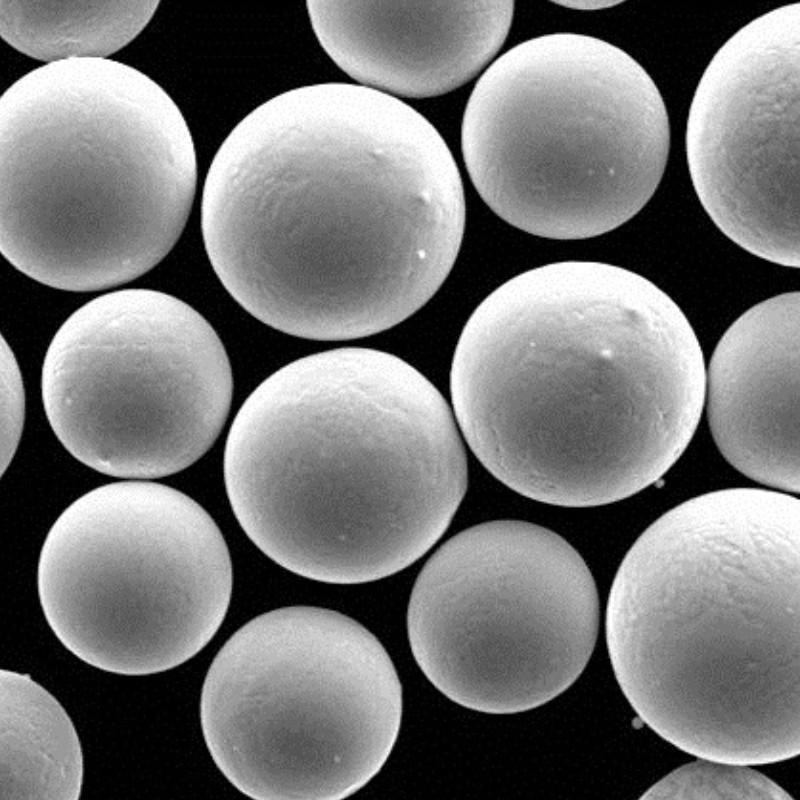
Better powder not only improves the effective mechanical performance of the parts, but also plays a large role in reducing production costs.
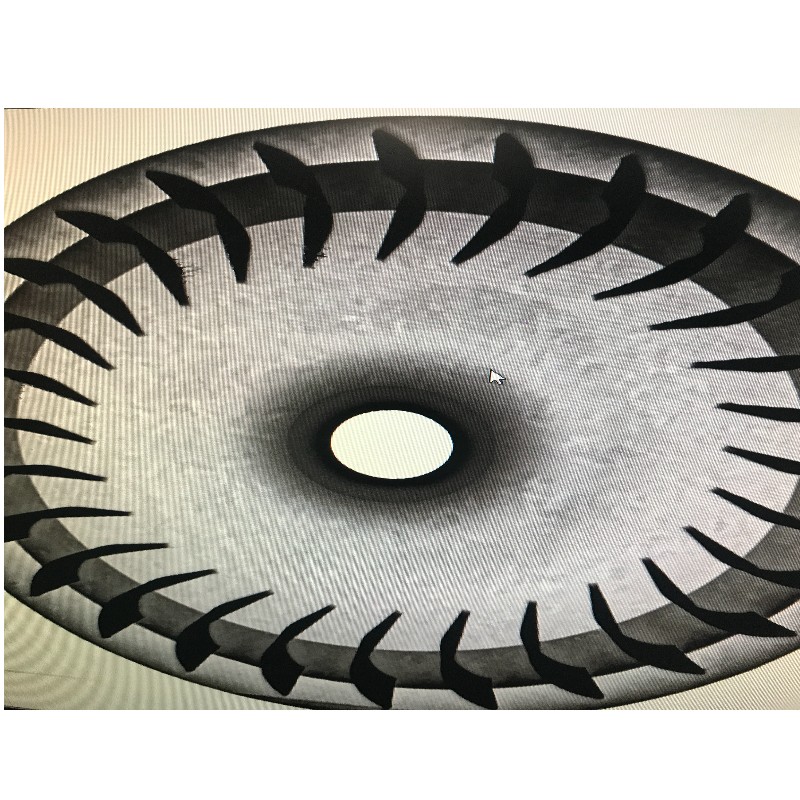
Even though the global movement to reduce greenhouse gas emissions is spurring a shift to renewable sources of energy, fossil fuels still generate 64 percent of today's electricity, according to The Brookings Institution. To meet the need for lower emissions, the energy industry is transitioning from coal and petroleum-based fuels to cleaner-burning natural gas. This shift is rapidly transforming power plants. Energy producers are revamping existing plants and building new facilities from the ground up. At the core of these new facilities are massive industrial turbines that convert natural gas into electricity. The turbomachinery industry is highly competitive and the marketplace demands increased fuel efficiency, power generation, system reliability with reduced maintenance costs, as well as manufacturing and supply chain efficiency. This fast-paced metamorphosis presents a potent opportunity for manufacturers of gas turbines — yet traditional manufacturing methods can't k
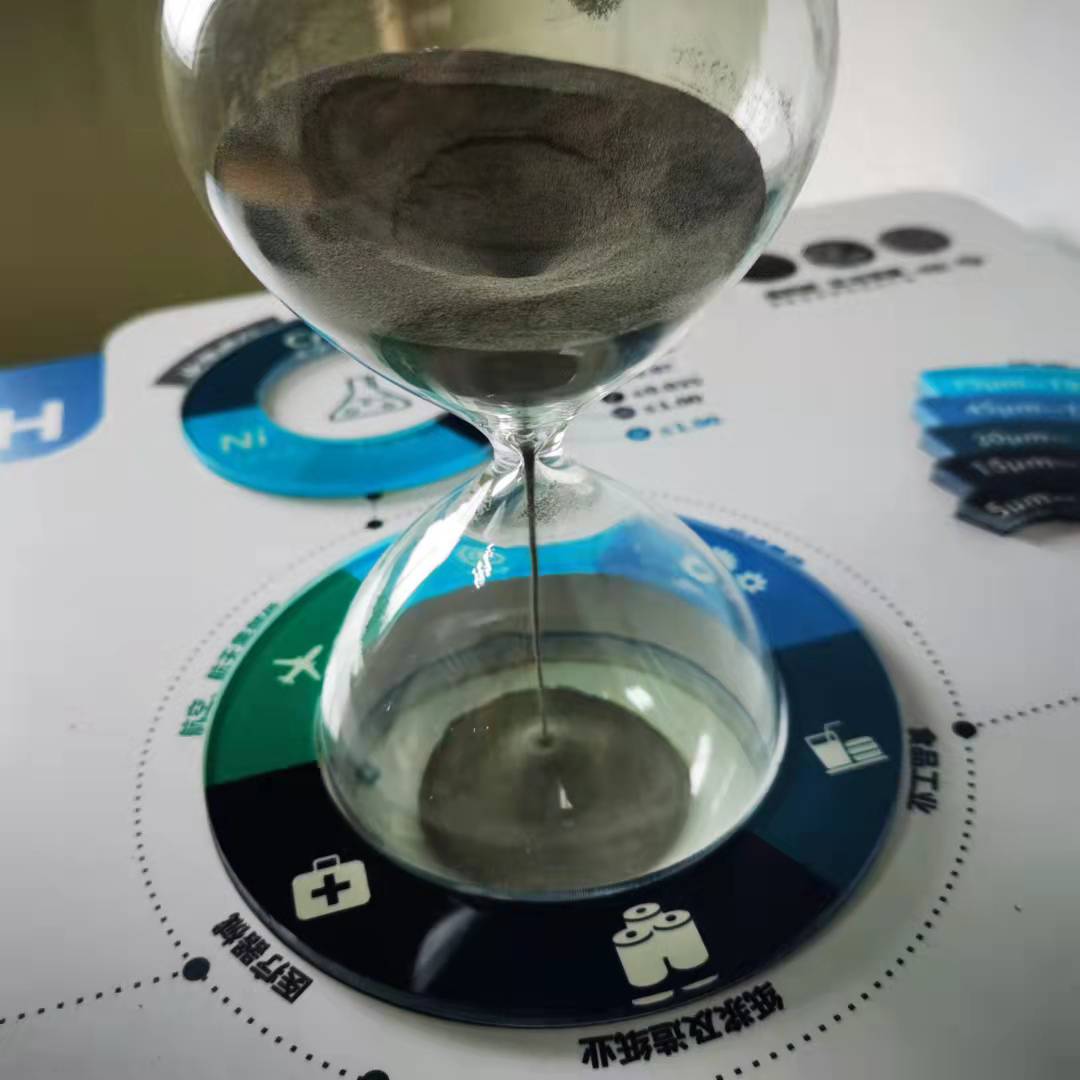
Additive Manufacturing (AM), also known as 3D printing, is a potentially transformative manufacturing technique. This process involves printing intricate, components to a tight specification which demands a high degree of consistency and repeatability in the feedstock. Controlling the performance of the powders is critical for both process efficiency and final product quality. How the powder is spread and distributed, as the layers are formed, are defining aspects of this performance. Variability in feedstock can lead to inconsistent bulk density, non-uniform layering, low tensile strength, poor surface finish and other part defects. The extent to which AM will shape the industrial landscape depends on the development of high-speed, precision machinery, and on the identification and consistent supply of powders able to meet the exacting demands of these machines. Increasingly the focus is turning to the powders themselves and how they can be optimised in an intelligent and